Competencias del especialista moderno de mantenimiento
Todas las organizaciones industriales persiguen una meta asociada a la máxima productividad y mínimo costo. Los equipos humanos responsables del mantenimiento de activos son una pieza clave en esa meta. Con alguna frecuencia, el poder controlar la tasa de fallos imprevistos en activos productivos, se constituye en una barrera casi infranqueable que imposibilita generar el beneficio esperado a partir del negocio. Cualquier actividad industrial está sujeta a evolución y el mantenimiento no está exento de esto. Cada vez más, nuevas metodologías y herramientas de análisis asociadas al mantenimiento industrial surgen, haciendo necesario una constante actualización al perfil profesional del mantenedor. La realidad es que no siempre el mantenedor cuenta con formación actualizada en las últimas tendencias del mantenimiento. (Estamos hablando de una formación de especialización, cuya oferta de capacitación es reducida en nuestra región). Se hace necesario, por lo tanto, que en los niveles gerenciales se diseñe una visión estratégica acorde con estas modernas tendencias y que se apoye al grupo de mantenimiento con la capacitación necesaria para poner en práctica esa visión. La meta de este proceso debe ser cumplir el sueño dorado del inversionista, cual es, producir con calidad, más y más, a un costo menor y menor. Es la única manera realista de generar una mayor rentabilidad: colocar el producto a un menor precio, e incrementar sus ventas; o bien, venderlo al mismo precio, pero generando más rentabilidad al tener menores costos. Mantenimiento es justamente una piedra angular de esta visión, al velar por la rentabilidad tanto hoy, como también mañana. (Goldratt, p. 120, 1993) Ahora bien, ¿cuál es ese conocimiento específico que el mantenedor requiere para el cumplimiento de los objetivos de su puesto y de la organización? A continuación, enumeramos algunas de las áreas temáticas que están teniendo más solicitud en las organizaciones que están en proceso de migrar hacia un mantenimiento de clase mundial.
Áreas temáticas con alta demanda de capacitación en las organizaciones industriales
Herramientas de análisis de fallas
Ante la necesidad de crear y optimizar un plan de mantenimiento, nos encontramos con que la visión actual de gestión de activos productivos está centrada sobre los modos de fallo. Acorde con Pistarelli (2010 p.22), el modo de fallo es la entidad suprema de la gestión del mantenimiento. A diferencia del enfoque tradicional en que la entidad suprema es el equipo (o el componente), hoy entendemos que no es posible la creación de planes de mantenimiento optimizados, sin antes comprender tan profundamente como sea posible, cuantas y cuáles son las diferentes maneras en que un componente puede fallar. Diferentes metodologías han sido desarrolladas para identificar, analizar y documentar modos de fallo de manera ordenada y estructurada:
- FMEA/FMECA: Failure Modes and effects analysis/ Failure Modes, and criticality analysis. Análisis de modos y efectos de fallo (o bien, Análisis de modos de fallo efectos y criticidad
- RCM: Reliability Centered Maintenance. Mantenimiento Centrado en Confiabilidad
- Análisis P-M: Physical Mechanism. Análisis de mecanismo físico de fallo.
- Árbol de Fallos.
- RCA: Root Cause Analysis. Análisis Causa Raíz.
Mantenimiento Detectivo y Riesgo industrial.
Industria crítica es un término utilizado para identificar instalaciones industriales cuyos fallos tienen una afectación no solo para esa organización, sino también para un grupo más amplio de personas (una población, un país o una región). La industria energética o de servicios públicos son claros ejemplos. Aquí los fallos implican un impacto que va más allá de la pérdida de producción asociada. El mantenimiento detectivo es una estrategia dirigida a controlar los fallos en dispositivos redundantes o de protección. Debe tratarse como un tipo de mantenimiento aparte por que la selección de las tareas de mantenimiento y la frecuencia con que se ejecutan, se sustentan en conceptos distintos:
- Tipos de redundancias y fallos ocultos
- Riesgo industrial
- Evaluaciones probabilísticas del riesgo
- Determinación del intervalo entre inspecciones
Ingeniería de Confiabilidad aplicada al mantenimiento Confiabilidad es definida como la probabilidad de que un componente opere sin fallas durante un tiempo específico. Es una disciplina muy amplia que abarca el diseño, la fabricación, y la operación de un activo. El ámbito del mantenimiento solo abarca la fase de operación. Los análisis de confiabilidad involucran el uso de funciones de probabilidad para determinar la probabilidad de fallo en un horizonte de operación específico. Además, son posibles también otros estudios, como estimar la probabilidad de un diagnóstico efectivo por parte de un especialista con cierto nivel de entrenamiento, o también análisis de estimaciones costo-riesgo para encontrar el escenario óptimo de un problema. Probablemente el aporte más importante en una organización, que la ingeniería de confiabilidad puede hacer (al menos inicialmente) es permitirle comprender con una base teórica a los responsables del mantenimiento, que los modos de fallo siguen distintos patrones de fallo, dependiendo de su naturaleza, y que, por ello, no todos los tipos de estrategias de mantenimiento (correctivo, preventivo, predictivo) son aplicables a todos los modos de fallo. El modelado matemático del comportamiento de la tasa de fallo para cada modo permite determinar cuál estrategia será técnicamente viable.
Mantenimiento Basado en Condición.
La naturaleza de esta estrategia de mantenimiento la hace más compleja y vasta, pero a cambio, se entiende que brinda la mejor relación costo-beneficio, sobre todo para aquellos modos de fallo cuyo impacto es relativamente grande. Tener la capacidad técnica para aplicar mantenimiento basado en condición implica contar con perfiles profesionales tales como: especialistas certificados de monitoreo de condición y ensayos no destructivos, Ingenieros de confiabilidad, técnicos certificados de adquisición de datos, gestores o facilitadores de programas de mantenimiento basado en condición. El mantenimiento basado en condición se basa en la ejecución periódica de inspecciones sobre la maquinaria y sistemas (ya sea utilizando los sentidos humanos o mediante tecnología) para la detección de anomalías en etapa de evolución, antes de que se produzca el fallo funcional. Es crítico que la detección sea lo suficientemente temprana como para poder coordinar acciones de mantenimiento en el momento oportuno. Entre mayor sea la complejidad del método de inspección usado, mayor será el requerimiento de capacitación para el especialista. Entre los métodos más usados mencionamos:
- Inspección visual
- Análisis de vibración mecánica
- Termografía infrarroja
- Análisis de aceite
- Ensayos no destructivos
- Análisis de parámetros eléctricos
Metodologías de optimización del mantenimiento
Se define así, a ciertos procesos estructurados de análisis y definición de estrategias de mantenimiento y operación que permiten mejorar el desempeño y resultados de los esfuerzos en mantenimiento.
El implementar este tipo de estrategias exige no solo al grupo de mantenimiento sino a muchos más actores en la organización, disposición al aprendizaje, dedicación, compromiso y una gran dosis de tenacidad y determinación para culminar los programas de implementación con buen suceso.
Un elemento en común que todas estas metodologías tienen es la estrategia de implementación basada en grupos multidisciplinarios de trabajo liderados por un facilitador. El facilitador es un especialista, entrenado y experimentado capaz de reproducir el proceso que exige la metodología y de liderar los análisis grupales hasta obtener el producto deseado en cada fase de análisis. Lamentablemente, algunas organizaciones se han apartado de este espíritu (tal vez por falta de conocimiento o una pobre asesoría, o por tener la intención de “ahorrar” algo de dinero en la fase implementación) y han encargado a una sola persona la ejecución de los análisis y la producción de los planes optimizados de mantenimiento. El resultado de este enfoque, en la abrumadora mayoría de los casos, es un resonante fracaso y un desperdicio de recursos y tiempo. En contraposición, los casos de éxito más relevantes han mostrado que una capacitación suficiente para los integrantes de los grupos multidisciplinarios más una formación mucho más intensiva para los facilitadores de los análisis, permiten fluir hasta obtener resultados que en ocasiones parecen bastante difíciles de creer.
Los métodos más importantes en este rubro son:
Mantenimiento Centrado en Confiabilidad.
Se trata de una metodología de análisis secuencial sobre los modos de fallo, a partir del establecimiento de un contexto operativo y un análisis de criticidad de cada sistema/equipo/componente. El uso de una herramienta de toma de decisión sobre la tarea de control/mantenimiento para cada modo de fallo es clave, y es el sello distintivo de esta metodología. Normalmente esa herramienta se llama: Árbol de decisión. El producto de este proceso es un plan de mantenimiento optimizado mediante criterios de confiabilidad. Puede ser aplicado en ausencia de un plan de mantenimiento, o para mejorar uno existente.
El RCM, es actualmente una de las metodologías de optimización más reconocidas, con numerosos casos de éxito. Además de permitir generar un plan de tareas de mantenimiento efectivas planteadas a partir del análisis de la naturaleza de la causa del fallo, otros beneficios que se pueden mencionar son:
- Genera un ambiente de trabajo en equipo en el que las habilidades y conocimientos del todo el personal tanto técnico como ingenieril es reconocido y aprovechado.
- Capacita a los integrantes de los análisis sobre la naturaleza de los fallos y su impacto en la organización
- Desarrolla en el personal una conciencia de costos y el beneficio de aplicar acciones proactivas
- Generar un procedimiento secuencial para la revisión periódica de los planes de mantenimiento Son muchas las organizaciones de primer nivel, que han adoptado al RCM como método estándar para la generación y revisión de planes de mantenimiento, tanto es así, que se ha creado los estándares SAE JA 1011 y SAE JA 1012, para normalizar los procesos de análisis de RCM, estándares que son citados como referencia en otros documentos IEC e ISO.
A pesar de la notoriedad que el RCM ha alcanzado y de los exitosos resultados que se han publicado, lamentablemente también son muchos los casos de organizaciones que han equivocado el camino al intentar implementarlo. Probablemente uno de los principales errores que se pueden señalar está en designar a un encargado que ejecute en solitario los análisis. Tal aproximación, además de limitada (el conocimiento de uno jamás será tanto como el de un grupo multidisciplinario) desaprovecha la potencia de la metodología para propiciar la transformación organizacional que se espera. Otro de los errores comunes es reducir la implementación de RCM a la adquisición de un software de automatización de los análisis. Si bien es cierto, una herramienta de software permite mejorar la productividad de los análisis, jamás debe ser considerada como un sustituto de los grupos de análisis multidisciplinarios.
Mantenimiento Productivo Total.
Implementar TPM (por las siglas en inglés de Total Productive Maintenance) excede ampliamente al área de Mantenimiento, requiere de la participación de muchos más niveles y sectores de la organización. El objetivo que persigue el TPM, es aumentar la eficacia integral de los activos fijos instalados y con ello la competitividad y flexibilidad de la empresa, mediante un enfoque a eliminar defectos de tipo crónico para alcanzar estándares de calidad y eficiencia supremos. Un objetivo indirecto es cambiar el comportamiento y la “cultura” de los empleados en términos de su empoderamiento y el nivel de involucramiento que ellos tienen en los procesos y el producto final.
La metodología se basa en la implementación de 8 pilares (no secuenciales, sino paralelos) que se indican a continuación:
- Mantenimiento Autónomo
- Mantenimiento Planeado
- Mejora enfocada
- Gestión temprana
- Mantenimiento para la calidad
- Capacitación y desarrollo
- Gestión de sectores administrativos
- Higiene, Seguridad y Medio Ambiente
A diferencia del RCM, el TPM no es una metodología secuencial, pero sí más integral, ya que toma en cuenta aquellos aspectos en los que otros sectores de la organización impactan en la productividad y competitividad de la instalación. Cada uno de los pilares requiere de su propio plan de implementación, siendo normalmente los primeros en ser implementados el mantenimiento autónomo (MA) y el mantenimiento planeado (MP). Normalmente la ejecución de programas TPM, están proyectados a más largo plazo que RCM y requieren de muchos más métodos, técnicas de implementación y recursos.
La discusión sobre cual metodología es mejor es frecuente en foros sobre temas de mantenimiento. Muy probablemente la respuesta es salomónica: ninguna de las dos es mejor que la otra, más aún, no tienen por qué ser excluyentes entre sí. Lo que sí parece ser cierto es que son las necesidades a corto, mediano y largo plazo las que influyen en la decisión sobre cuál de las dos metodologías implementar. El propósito del RCM es bastante específico: crear u optimizar un plan de mantenimiento bajo criterios costo-riesgo-beneficio. El TPM en cambio procura un cambio cultural en muchas otras áreas, la principal de ellas es el involucramiento del personal operativo en labores de mantenimiento básicas, para las cuáles tengan el apropiado entrenamiento. El TPM no está enfocado en optimizar la planeación del mantenimiento. Si ésta es una necesidad, lo mejor sería apoyarse en RCM para esto y dejar que los demás pilares de TPM trabajen en sus propios objetivos como metodología, a un mayor plazo de tiempo de lo que el RCM comienza a producir resultados.
Administración y Programación del Mantenimiento
Hasta el momento se ha hablado de actividades, métodos y herramientas para la planeación del mantenimiento. Pero ¿qué hay de la ejecución de todo ello? ¿Cómo se recaba la información sobre los fallos? ¿Cómo se programan y preparar actividades de mantenimiento necesarias para garantizar el cumplimiento del plan? A continuación, alguna de las destrezas y conocimientos deseables en el grupo de mantenedores encargados de esta fase:
- Registros en Mantenimiento, codificación y taxonomía. Manejo de sistemas informáticos de mantenimiento
- Programación de tareas de mantenimiento, coordinación de paradas de planta, supervisión de reparaciones
- Gestión de órdenes de trabajo, registro de la información de fallos, reportes de paradas e indicadores
- Gestión de inventarios
Perfil de competencias de los funcionarios de mantenimiento
Definir las competencias del personal de mantenimiento, para luego, en caso de no cumplirse los resultados o expectativas, decir simplemente que la persona: “no cumple con el perfil del puesto” es relativamente frecuente en nuestro medio. Uno de los desafíos más relevantes de la gerencia de mantenimiento es identificar fortalezas y debilidades de su personal y contraponerlo contra la visión de gestión que el negocio le impone, para luego propiciar la transferencia metodológica y de conocimiento necesario para cumplir cabalmente con esa visión. No obstante, nadie puede esperar que esta responsabilidad sea asumida por una sola persona, sino que se hace indispensable la activa participación de profesionales especialistas en el tema. En materia de proyectos de formación y capacitación de especialistas de mantenimiento, la participación y colaboración del área de Recursos Humanos tiene mucho que ofrecer.
Como se dijo anteriormente una responsabilidad fundamental del líder del grupo de mantenimiento es identificar vacíos y proporcionar los recursos necesarios para cubrir la matriz de competencias ya sea con capacitación, con asesoría continuada o bien con servicios externos por parte de especialistas. La estrategia dependerá, por supuesto, del tamaño de la organización y la cantidad de activos dentro del plan de mantenimiento.
El siguiente cuadro no pretender ser una matriz de competencias en el amplio sentido de la palabra, dado que algunos elementos que han quedado fuera (sobre todo para el personal encargado de las tareas de intervención de máquina, que requieren de habilidades y conocimientos muy específicos). Está sobre todo enfocado en algunas habilidades que el personal encargado de la parte de gestión y planeación del mantenimiento debe abordar acorde con las últimas tendencias del mantenimiento.
Tabla 1. Matriz de competencias exigidas por las más modernas tendencias en gestión de mantenimiento.
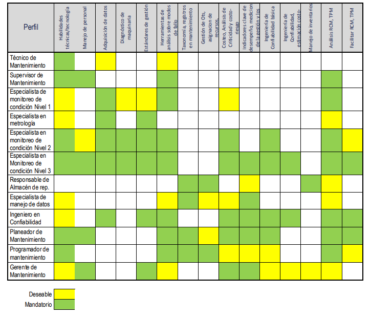
Conclusiones
Es un error suponer que la evolución en la gestión de mantenimiento obedece solamente al avance tecnológico. Las prácticas y metodologías de análisis y gestión han evolucionado también modificando el perfil de puestos característicos en esta disciplina. El advenimiento de la ingeniería de confiabilidad y de las metodologías de optimización, exigen no solamente la presencia de gestores calificados en estos temas, sino que, además, es deseable que los demás constituyentes del grupo de mantenimiento tengan un conocimiento ya sea general o más específico en estos temas, en orden a participar activamente de los análisis o ejecutar apropiadamente tareas identificadas en tales procesos de optimización.
Aunque es deseable que personal de mantenimiento cuente con los conocimientos generales que su puesto le demanda desde su formación académica, lo cierto del caso es que frecuentemente toca a las organizaciones industriales complementar ese conocimiento con proyectos de formación y capacitación para sus colaboradores. Tales proyectos deben estar diseñados a partir de una matriz de competencias contemplando no solamente eventos formales de capacitación, pero también actividades complementarias de seguimiento, evaluación de resultados, asesoría en campo, “coaching” personal y en algunos casos, actividades orientadas al tratamiento del manejo del cambio.
De especial atención resulta la implementación de metodologías de optimización y métodos de diagnóstico de fallos, cuya curva de aprendizaje normalmente prolongada (debido a la complejidad tanto de los métodos de inspección y diagnóstico, como de la naturaleza con frecuencia multivariable del modo de fallo), haciendo necesarios programas continuados de capacitación, seguimiento y medición de lo implementado a partir de los conocimientos adquiridos.
Referencias Bibliográficas
Goldratt, Elihayu M. (1993). La Meta. Díaz de Santos S.A
Pistarelli, Alejandro (2010). Manual de mantenimiento: Ingeniería, Gestión y Organización. Buenos Aires.