SOBRE EL AUTOR
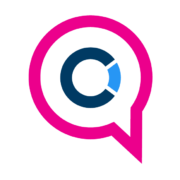
Integridad Mecánica es el proceso de garantizar que los equipos sean fabricados con los materiales adecuados de construcción y, además, sean correctamente instalados, mantenidos y reemplazados para evitar fallas y daños ambientales. También puede definirse como el manejo crítico de los equipos de proceso para asegurarse que sean diseñados e instalados apropiadamente y que su operación y mantenimiento se lleven a cabo correctamente.
Integridad Mecánica es apenas uno de los catorce elementos incluidos en el estándar OSHA 1910.119 – Gestión de Seguridad en los Procesos (GSP).
La Integridad Mecánica se aplica a equipos tales como recipientes a presión, tanques de almacenamiento, sistemas de tuberías y sus asociados (válvulas, conexiones, etc.), dispositivos de alivio, paradas de emergencia y sistemas de control (incluyendo dispositivos para monitoreo, sensores, alarmas y enclavamientos) y bombas, sopladores y compresores del mismo sistema.
En cualquier industria, siempre hay una imperiosa necesidad por aumentar la seguridad, reducir el riesgo y aumentar así el rendimiento y la confiabilidad en las operaciones.
La Gestión de Seguridad en los Procesos se puede definir como la aplicación metodológica de sistemas de gestión y de control, de una forma tal que todos los riesgos existentes y potenciales sean identificados, analizados, evaluados y controlados, con la finalidad de prevenir cualquier tipo de incidente que pueda afectar a los procesos.
Según lo indicado por el estándar de Gestión de Seguridad en los Procesos: “Los elementos de un programa de Integridad Mecánica incluyen la identificación y clasificación de los equipos y su instrumentación, el desarrollo de procedimientos escritos para su mantenimiento, la capacitación para ejecutar las actividades de mantenimiento, las inspecciones y pruebas, la corrección de deficiencias en los equipos que estén fuera de los límites aceptables y definidos en la información de seguridad del proceso y, el desarrollo de un programa de aseguramiento de la calidad”.
Para una instalación industrial, lo anterior significa lo siguiente:
Cuando se viaja a través de la implementación de un sistema de gestión de Integridad Mecánica, es habitual encontrarse con la presencia de un número muy importante de Normas Internacionales interrelacionadas e interdependientes entre sí, formando una compleja red de estándares. La gestión de Integridad Mecánica comprende las actividades necesarias para garantizar que equipos (activos) sean diseñados, fabricados, instalados, operados y mantenidos de tal manera que proporcionen el rendimiento deseado de manera segura y confiable, sin afectar la salud y el medio ambiente. Aquí aparece la primera relación, en este caso, con la serie de normas ISO 14000 e ISO 18000. La palabra “activo” se usa como sinónimo de equipo; la idea es rápida y fácilmente introducir la relación con la serie de gestión de normas ISO 55000.
La Integridad Mecánica comienza con la preparación de una Lista de Equipos críticos para la seguridad del proceso. Un análisis de riesgos debe aplicarse para definir la criticidad de los equipos de acuerdo con API 580-581. El equipo debe codificarse siguiendo una nomenclatura estándar definida por la instalación. El código debe permitir la búsqueda por clase de equipo. La clase de equipo y especificaciones deben seguir ISO 14224.
Cuando se implementa un sistema de gestión de Integridad Mecánica, todos los programas de mantenimiento preventivo se establecen, financian y asignan personal en niveles suficientes para evitar la necesidad de un mantenimiento por “equipo fallado”.
Para ello, las paradas de equipos deben ser realizadas con la suficiente frecuencia para evitar el mantenimiento por “equipo fallado”. Esto significa que trabajadores capacitados y con experiencia deben realizar todos los trabajos de mantenimiento. Junto con esto, los requisitos y la documentación de la capacitación de contratista deben ser equivalente a la de los empleados regulares. Además, al final, todo trabajo de mantenimiento debe hacerse con equipos y procedimientos de instalación adecuados, y con dispositivos de seguridad de acuerdo con normas y códigos aplicables. Para lograr lo anterior, las empresas deben crear procedimientos y programas sobre:
La instalación deberá establecer e implementar procedimientos escritos para mantener la integridad continua de los equipos de proceso. Los procedimientos de reparación o mantenimiento preventivo de los equipos pueden ser extraídos de las instrucciones del fabricante del equipo y luego ser optimizados con la experiencia de los técnicos. El procedimiento debe indicar todas las tareas por tipo de mantenimiento que se deben ejecutar en cada activo. Cada procedimiento debe seguir el Sistema de Control de Documentos de acuerdo con ISO 9000 e ISO 55000.
La instalación deberá desarrollar un Análisis de Brechas de Capacitación para Integridad Mecánica. La capacitación para Integridad Mecánica debe ser una combinación de habilidades generales, competencias y entrenamiento específico. La capacitación en habilidades generales sería a todo lo largo de las líneas de artesanía típicas: tubero, soldador, ayudante, técnico instrumentista, etc. La capacitación específica incluye certificaciones para inspecciones internas en recipientes y tanques, reparación de dispositivos de alivio y soldadura. Estos requisitos también aplican a contratistas que pueden llevar a cabo las actividades de Integridad Mecánica para todo el proceso. Este requisito debe cumplir con ISO 9001, ISO 55000 y OSHA 1910.119.
Los remanentes trece elementos de Gestión de Seguridad en los Procesos (OSHA 1910.119) deben cumplirse en cada etapa del sistema de gestión de Integridad Mecánica.
En conclusión, un número muy importante de Normas Internacionales, interrelacionadas e interdependientes entre ellas, han desarrollado una compleja red de normas alrededor de la gestión de Integridad Mecánica. Afortunadamente, esta es la manera más segura para evitar fallas catastróficas, explosiones, impactos ambientales y lesiones personales en instalaciones industriales.