LA OTRA VISIÓN DE LA CONFIABILIDAD OPERACIONAL
APLICABILIDAD DE LA METODOLOGÍA JERARQUIZACIÓN DE ACTIVOS POR ANÁLISIS DE CRITICIDAD
“MÉTODO DE LOS PUNTOS Y FRECUENCIA DE FALLA”
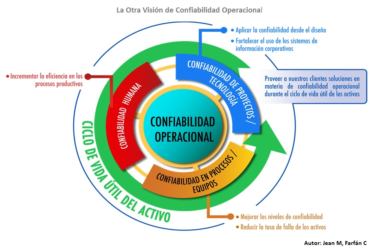
La Otra Visión de la Confiabilidad Operacional desde una perspectiva simplista y de fácil comprensión al lector, en el artículo anterior se explicó la aplicación del método de los puntos y el índice de probabilidad de falla (IPF), para determinar la criticidad en un sistema de tuberías que transporta petróleo.
En la continuación de la aplicación de los análisis de criticidad, este documento (3era parte) se explicara el método de los puntos y la frecuencia de falla (FF), para determinar la criticidad en un conjunto de instalaciones petroleras que procesan fluido multifasico (crudo, gas y agua) en Venezuela, dichos sistemas de manera general se pueden mencionar, como el conjunto de activos que realizan las funciones básicas de operar y mantener con los mayores estándares de eficiencia de empresas de primer nivel.
Dichos activos son: (Pozos, múltiples de recolección, oleoductos, gasoductos, acueductos, separadores, depuradores, enfriadores, despojadores de líquidos, fosas API, torre de absorción, intercambiador de calor, rehervidor bombas, unidades de medición fiscal, filtros, deshidratadores, tanques de estabilización, almacenamiento, compresores, motores, turbinas, generadores eléctricos, mechurrios, que realizan el proceso macro de extraer, manejar, disponer, almacenar y transportar el fluido (petróleo, gas y agua) extraído de los yacimientos para su uso en el mercado interno como su venta en el exterior.
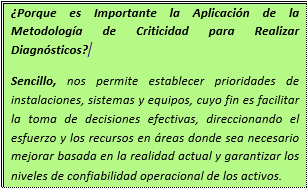
Palabras Claves: Activo, contexto operacional, confiabilidad operacional, criticidad, custodios de instalaciones, estrategias de mantenimiento, frecuencia de falla, instalaciones, sistemas y equipos.
Abreviaturas y términos. AC: Análisis de criticidad. ENT: Equipo natural de trabajo. FF: Frecuencia de falla. MBND: Miles de barriles día de petróleo. MMPCND: Millones de pies cúbicos normal día de gas. MBA: Miles de barriles de agua. TPFS: Tiempo promedio fuera de servicio.
Repasando algunas Definiciones básicas a tener presente en el mundo de la Confiabilidad Operacional y el Mantenimiento, se tienen:
Activo: Es un elemento tangible o intangible, capitalizable en un ciclo de vida establecido, que cumple una función en un proceso productivo y está sujeto a acciones de mantenimiento [1].
Contexto Operacional: Es el conjunto de circunstancias que condicionan la operación de un equipo o sistema, están definidas como: localidad, ambiente, fluido de servicio, parámetros de operación, lineamientos ambientales, de seguridad y producción, calidad y disponibilidad de los insumos requeridos, configuración de trabajo, flexibilidad operacional, redundancia, alarmas, monitoreo de primera línea y otros. [1].
Custodio de Instalación: Es el ente encargado de velar por el funcionamiento de los activos dentro de los parámetros operacionales establecidos, con el fin de lograr el producto bajo las especificaciones requeridas. [1].
Datos del Equipo: Son los parámetros técnicos, operativos y ambientales que caracterizan el diseño y la utilización de una unidad de equipo. [1].
Equipo: Es un elemento de producción dentro de un arreglo lógico funcional que cumple con los siguientes criterios:
- Está sujeto a planes de mantenimiento.
- No es componente, parte o pieza (ejemplos: sello mecánico, manómetros, haz de tubo, tarjeta electrónica, entre otros).
- El valor de reemplazo es mayor que el costo de mantenimiento.
- Es trazable en el tiempo.
- Está sujeto a un control de gastos ocasionados por la aplicación de mantenimiento correctivo, preventivo, proyectos de mantenimiento y paradas de planta. [1].
Estrategia de Mantenimiento: Son un conjunto de lineamientos o directrices que definen la forma en cómo se lleva a cabo el mantenimiento (asegura una decisión óptima). [1].
Falla: Es la terminación de la habilidad de un sistema/equipo/parte para realizar una función requerida [2].
Función: Es la capacidad de un elemento o activo de brindar un determinado servicio según las condiciones de trabajo, respetando su diseño. [1].
Instalación: Es el tercer nivel de la estructura taxonómica que hace referencia al macroproceso productivo, localización o disposición geográfica. [1].
Modo de Falla: Es cualquier evento que genera una falla funcional [3].
Mantenimiento: Es una combinación de todas las acciones técnicas y administrativas, que pretenden retener o restaurar un activo en un estado en el que pueda ejecutar una(s) función(es) requerida(s). [1].
Mantenimiento: Combinación de todas las acciones técnicas y de gestión destinadas a retener o restaurar un elemento en un estado que puede realizar y requiere. [2].
Planta / Unidad: Es el cuarto nivel de la estructura taxonómica que hace referencia a un proceso productivo que integra la instalación. [1].
Sección / Sistema: Es el quinto nivel de la estructura taxonómica que hace referencia a las subdivisiones que componen una planta o unidad. [1].
Sub-Sección/Sub-Sistema o Lazo: Es el nivel 5.1 de la estructura taxonómica, definido en la Norma Técnica PDVSA MM–01–01–07, que se establece para ser utilizado según la complejidad de la organización y el contexto operacional que requiera un nivel de detalle adicional a los cinco niveles previos. Ejemplo: sub–sistema de ventilación, sub–sistema de bombeo, sub–sistema de alimentación, lazo de control, entre otros. [1].
Tiempo Promedio Entre Fallas (TPEF): Es el tiempo promedio entre una falla y otra, éste incluye el tiempo fuera de servicio. [1].
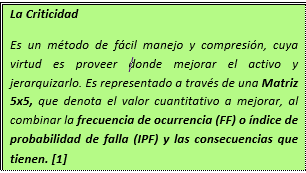
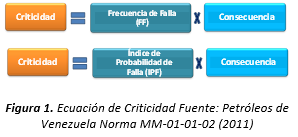
Consecuencias
Resultado de un evento. Puede existir una o más consecuencias de un evento, las cuales sean expresadas cualitativa o cuantitativamente. [1]
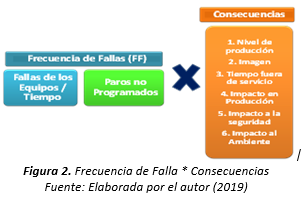
El caso de estudio presentado, se realizó para calcular la criticidad (AC) utilizando el método de los puntos y la frecuencia de falla (FF).a un conjunto de instalaciones de un Campo Petrolero en Venezuela, con una producción manejada de 187 mil barriles normales día de petróleo (MBND) con una gravedad 23 °API.
De manera general se presenta el esquema de las Plantas de producción de petróleo (extracción de fluidos, manejo, disposición, almacenamiento y transporte) sujetas al estudio. Tal y como se muestra en la figura 3.
A continuación, se muestra el esquema macro de las Plantas de producción de petróleo sujetas al estudio de criticidad por frecuencia de falla (FF).
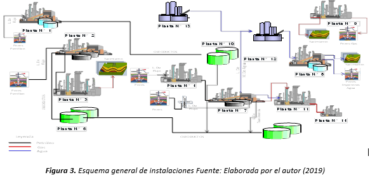
Una vez conocido el entorno del sistema a estudiar, definido el objetivo, alcance y conformación del ENT, se procede a describir de manera clara y sencilla El Contexto Operacional del activo sujeto al estudio de la siguiente manera:
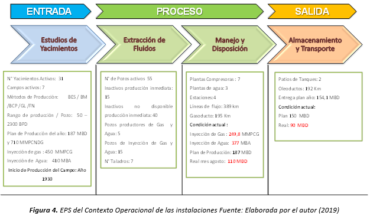
Los valores de frecuencia de falla (FF) y las consecuencias de cada equipo son determinados en la matriz 5×5, en base al comportamiento y características del sistema bajo análisis, estableciéndose los siguientes niveles.
El color rojo es el nivel de Alta criticidad = A; color amarillo es el nivel de Media criticidad= M y el color verde es el nivel de Baja Criticidad= B.
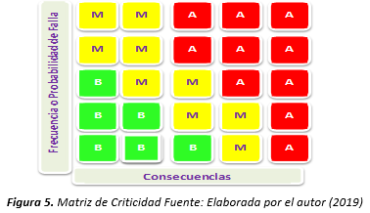
A continuación, se muestra el flujograma con las actividades principales a realizar para el estudio de criticidad, es de resaltar que estaremos utilizando el método de los puntos y la frecuencia de falla (FF), para ello se detallan algunas premisas:
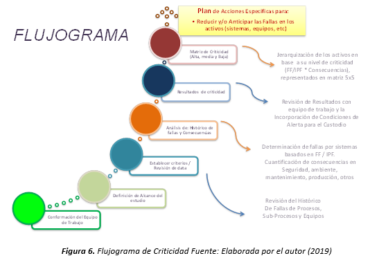
Premisas del estudio
- Frecuencia de Falla (FF): Es la cantidad de eventos (Fallos) suscitados en el activo con afectación al sistema productivo.
Nota: Los valores de FF y TPFS fueron tomados principalmente de los indicadores técnicos de confiabilidad correspondientes al año de estudio, y para aquellas instalaciones que no se les llevan el registro histórico, la data fue generada del ENT y revisión del libro de operadores y mantenedores.
- Tiempo promedio fuera de servicio (TPFS): Se estimó que el tiempo para reparar una falla frecuente mide la efectividad en restituir la unidad a condiciones óptimas de operabilidad una vez que la unidad queda fuera de servicio por una falla, dentro de un tiempo considerado para el estudio.
- Nivel de producción: Esta directamente asociado a la capacidad de producción diaria de la unidad de proceso estudiada, en las condiciones de operación existentes.
- Impacto en producción: Se consideró el porcentaje de producción que se ve afectada cuando ocurren fallas en el sistema estudiado.
- Costo de reparación: Se estimó el costo promedio para reparar las fallas del sistema estudiado y así restituir su función. Incluye todos los costos que se incurren para corregir las fallas, como labor, materiales y transporte, a una paridad cambiaria para los cálculos fijado por el Banco Central de Venezuela (BCV). Este costo fue considerado de acuerdo a información suministrada por el equipo de Ingeniería de Costos.
- Impacto en la seguridad personal: representa la posibilidad de que sucedan eventos no deseados que ocasione lesiones, heridas o fatalidades del personal.
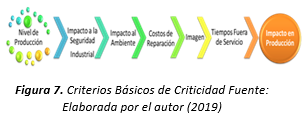
- Impacto Ambiental: representa la posibilidad de que sucedan eventos no deseados que ocasione la violación de cualquier regulación ambiental.
Una vez definido todos los elementos procedemos al cálculo de la criticidad, utilizando la plantilla diseñada para el sistema en estudio (Ver anexo 1), donde ya está calibrado por el método de los puntos la ponderación de cada variable, finalmente se procede al cálculo de la criticidad aplicando la siguiente formula:
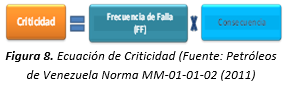
Ya realizado los pasos previos descritos en el flujograma mostrado en la figura 6, el estudio se presenta preliminarmente ante el ENT para revisar y validar los resultados de la criticidad.
A continuación, se muestran los resultados por proceso (Crudo, Gas y Agua) de la aplicación de criticidad utilizando la frecuencia de falla (FF), representados en una matriz 5 x 5.
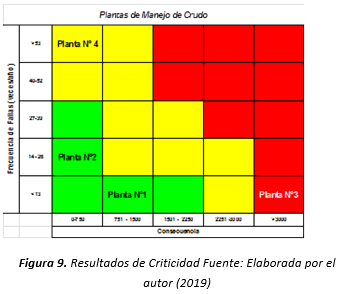
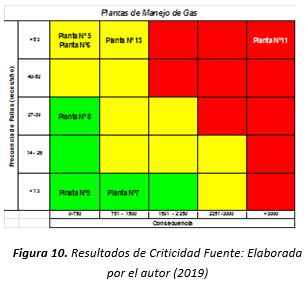
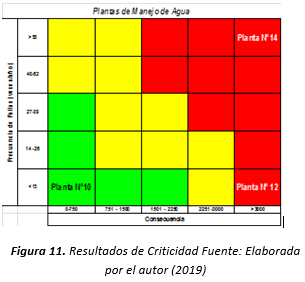
Ya finalizado este paso (Matriz 5×5), el ENT genera un listado de alertas y acciones con la finalidad de facilitar la toma de decisiones efectivas, direccionar el esfuerzo y los recursos en áreas a mejorar en el corto, mediano y largo plazo.
ANÁLISIS DE RESULTADOS
- Para el caso de las Plantas de manejo de Crudo sus principales problemas son: Deshidratación, enfriamiento, tratamiento anticorrosivo y control de corrosión.
- Plantas de manejo de Gas sus principales problemas son: Alto número de fallas en moto-compresores asociados por: Lubricación, compresión, monitoreo y control. desfase en la realización de los mantenimientos niveles III y IV, procura de repuestos menores y consumibles y regulación de válvulas de control de inyección de gas a pozos.
- Plantas de manejo de Agua sus principales problemas son: Alto número de fallas en motores, turbinas (desplazamiento axial) y bombas (Sellos), agua fuera de especificaciones, falta de inyección de productos químicos en los sistemas de filtración.
CONCLUSIONES
En base a la volumetría de instalaciones estudiadas (14), se tiene que 4 activos están en alta criticidad, 4 en media y 6 en baja criticidad.
- En alta criticidad dos (2) plantas de manejo de agua, una (1) crudo y una /1) de gas.
- Media criticidad tres (3) plantas de gas y una (1) de crudo.
- En baja criticidad tres (3) plantas de gas, dos (2) de crudo y una (1) de agua.
- Con la determinación de la criticidad, se está anticipando a probables fallas que puedan afectar los objetivos de producción, el presupuesto, la seguridad, salud, ambiente y a la comunidad, ya que permitirá mejorar los procesos.
PLAN DE ACCIÓN
- Establecer las estrategias a corto plazo para las Plantas que se encuentran en criticidad alta. Responsables: Operaciones y Mantenimiento.
- Retomar el plan de inspección preventivo establecido por la organización y controlar factores de impacto tales como: verificación de condición y tipo de revestimiento en el que presenten aislamiento eléctrico. Responsables: Operaciones y Mantenimiento.
- Garantizar los recursos para el cumplimiento de las acciones de mejora planteadas.
- Seguimiento y control en el cumplimiento de las acciones y Planes de Mantenimiento.
- Colocar en funcionamiento el sistema de filtrado de la planta de manejo de agua.
- Impulsar los procesos de procura de materiales y consumibles para la ejecución de los mantenimientos preventivos establecidos en los planes de cuido del activo.
- Acelerar los procesos de contratación de actividades medulares de acuerdo al contexto operacional y la criticidad de las instalaciones.
- Someter la adquisición de emergencia de productos químicos para el proceso de producción (demulsificantes, antiespumantes, dispersantes, anticorosivos, otros).
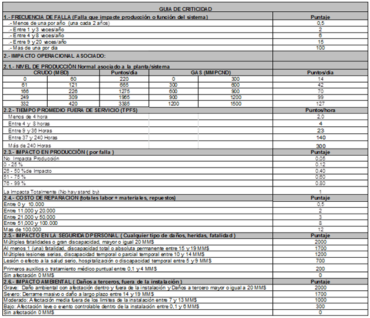
Bibliografía
[1] Petróleos de Venezuela (2011) Norma MM-01-01-01 Definiciones de Mantenimiento y Confiabilidad.
[2] Estándar internacional ISO 14224:2016.
[3] SAE JA-1011 año 2011
[4] Petróleos de Venezuela (2011) Norma MM-02-01-01 Jerarquización de Activos por Análisis de Criticidad).
[5] El Análisis de Criticidad, una Metodología para mejorar la Confiabilidad Operacional. https://reliabilityweb.com/sp/articles/entry/el-analisis-de-criticidad-una-metodologia-para-mejorar-la-confiabilidad-ope/
[6] Análisis de criticidad de plataformas Activo Integral Cantarell PEMEX Exploración y Producción Desarrollo e Implementación de un Modelo de Variables de Estado de Equipos y Estructuras Jorge Enrique Martínez Frías a, Andrés Eduardo Rivas b, Richard J. Matthews c Departamento de Integridad Mecánica y Confiabilidad PIMS Of London LTD. (https://docplayer.es/14054076-Analisis-de-criticidad-de-plataformas.html)
[7] Análisis de criticidad parte 1 y 2 http://a3consultraining.com/analisis-de-criticidad-de-activos-parte-1/.
[8] La Otra Visión de la Confiabilidad Operacional Aplicabilidad de la metodología jerarquización de activos por análisis de criticidad “2 da parte aplicabilidad del método de los puntos e índice de probabilidad de falla”. (2019 por Jean Farfán).
[9] La Otra Visión de la Confiabilidad Operacional Aplicabilidad de la metodología jerarquización de activos por análisis de criticidad “1 era parte definiciones básicas, métodos de cálculo y beneficios” (2019 por Jean Farfán).
Resumen Laboral del Autor
Ingeniero en Mantenimiento Mecánico con 14 años de experiencia. Área Profesional: Confiabilidad Operacional, Mantenimiento, Sistema Integrado de Gestión y Transporte Terrestre, en la Industria Petrolera Nacional (PDVSA División Furrial).
Experiencia con PDVSA INTEVEP para la elaboración, revisión y actualización de normas PDVSA tales como: Modelo de gerencia de mantenimiento. Definiciones de mantenimiento y confiabilidad. Niveles de mantenimiento. Estructura de activos (Jerarquización de sistemas y taxonomía de equipos en PDVSA). Guía para definir la estructura de activos en PDVSA. Indicadores de gestión del proceso de mantenimiento.
Estudios: Especialización en Finanzas, Diplomado en Gerencia de Mantenimiento Industrial. Diplomado en Análisis Probabilístico de Riesgos en Proyectos de Exploración y Producción. Especialización en Ingeniería de Mantenimiento.
Correo electrónico: ljmfl7788@gmail.com
Contacto Móvil: +584249431320